Home > Workforce management
Workforce Management
Workforce management (WFM) is a set of processes whose aim it is to increase productivity and raise levels of welfare within the company by managing workers in a coordinated, efficient and safe manner.
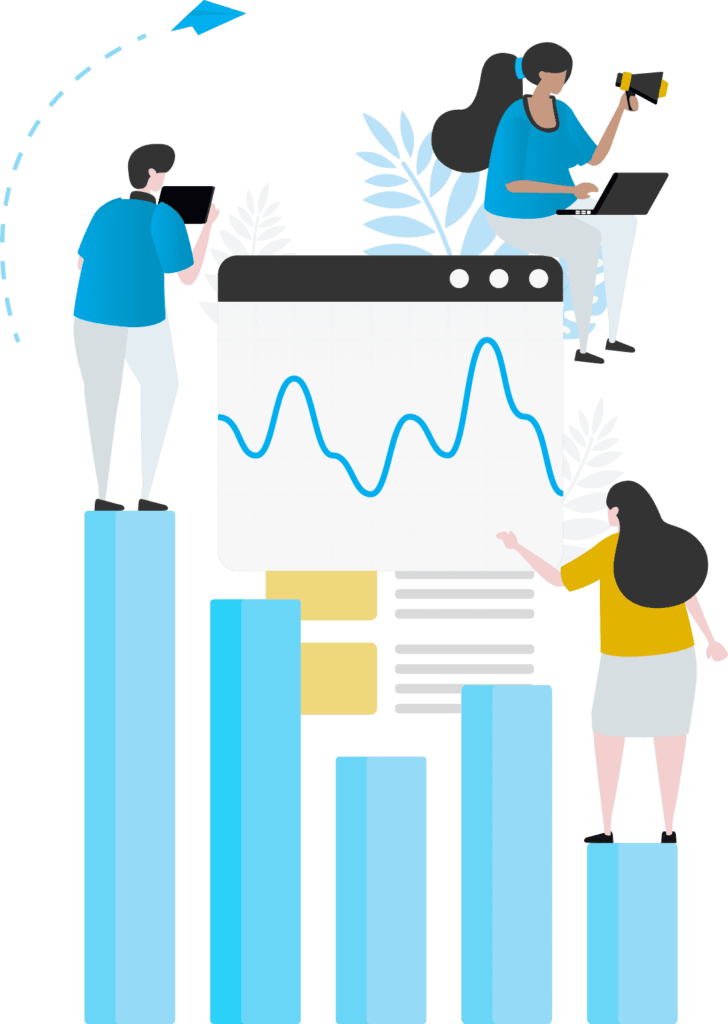
What is workforce management?
Workforce management (WFM) is a set of processes whose aim it is to increase productivity and raise levels of welfare within the company by managing workers in a coordinated, efficient and safe manner.
A workforce-management system is a digital solution which allows you to plan and manage people’s work inside a factory. Seamlessly fitting in with corporate procedures and taking into account the company’s set targets, it is able to facilitate or automate task assignment to the most suitable operator.
Why workforce management is important
WFM is an essential link between people management on an administrative level and production activities on the factory floor.
What we mean is that it closes the gap between two worlds which have been separated so far (staff management and production), pooling information and making production activities as streamlined and flexible as possible.
By bringing together all the information about people management on an administrative level and production activities, workforce management allows you to have the right person in the right place at the right time. This raises efficiency, reduces compliance risks and improves people’s sense of satisfaction.
What is more, when you use a WFM system, you help to increase customer satisfaction as well because you acquire a clearer picture of staff needs in real time, higher employee engagement levels and, as a result, greater respect of production plans.
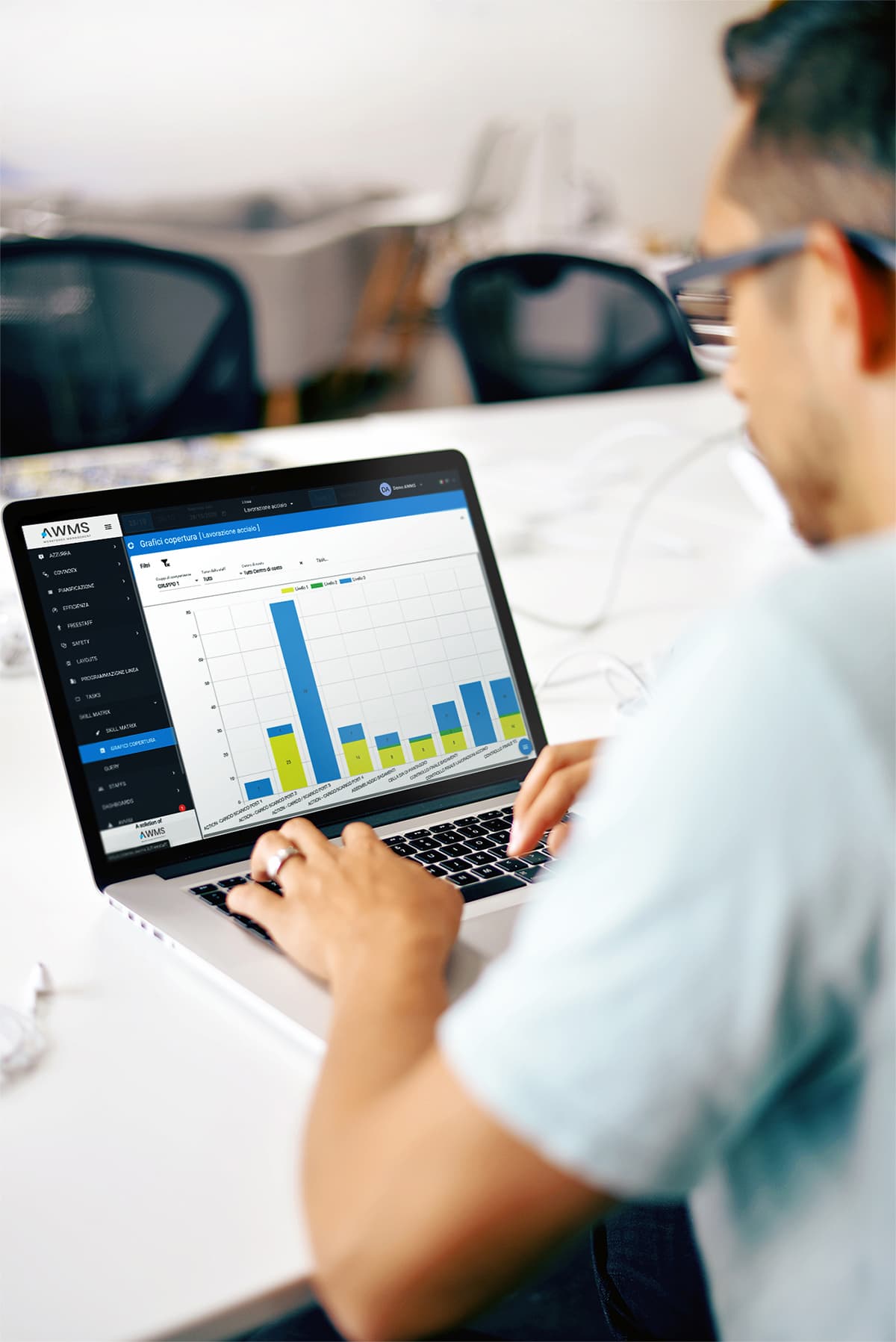
The advantages of using workforce-management software
Using WFM software enables companies to better manage their workforce by time optimisation, tighter organisation and more streamlined processes. All of this leads to immense advantages, such as:
- Increased productivity. By mapping out staff skills, the team leader can allocate the most suitable person to each workstation, thus optimising the production system.
- Reduction in costs. Optimal worker scheduling reduces unplanned overtime costs by 33%.
- Shared data in real time. An integrated WMF system means that all the information you need about workers is updated in real time and made available to you, allowing you to capitalise on that knowledge.
- A single point of contact. All scheduling is carried out comprehensively by the WFM software, thus supplanting all other non-integrated systems and paper-based methods.
- An upturn in professional gratification. When activities are allocated to staff members on the basis of their skills and limitations, you automatically acknowledge their strong points and this is a source of gratification for them.
- Greater safety. Scheduling takes into account all regulations about health and safety in the workplace, thus mitigating any risks of accidents and safeguarding the company.
- Better communication. Team leaders and factory workers can communicate through a single system in a straightforward and quick manner and there is also the option of gathering worker feedback and sending mass or targeted messages.